Una nueva forma de fabricar acero podría limpiar el CO2 de la siderurgia
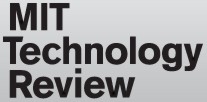
La técnica de Boston Metal podría acabar con las emisiones de una de las industrias más contaminantes del mundo. Pero si que funciona a precio asequible y escala industrial, aún tendrá que convencer a los dinosaurios del sector para que cambien su proceso de producción por James Temple | traducido por Ana Milutinovic Un tosco
La técnica de Boston Metal podría acabar con las emisiones de una de las industrias más contaminantes del mundo. Pero si que funciona a precio asequible y escala industrial, aún tendrá que convencer a los dinosaurios del sector para que cambien su proceso de producción
por James Temple | traducido por Ana Milutinovic
Un tosco disco de acero de color gris oscuro cubre un banco del laboratorio de Boston Metal, una spin-off del MIT ubicada a media hora del instituto, al norte de Boston (EE.UU.).
Este disco representa el primer lote de una aleación de alta resistencia de la compañía, fabricada mediante un innovador proceso de producción de metales. En lugar del alto horno que la industria lleva usando durante siglos, Boston Metal ha desarrollado un mecanismo que se parece más bien a una batería. Es lo que se conoce como célula electrolítica, un dispositivo que emplea electricidad, en vez de carbono, para procesar el mineral de hierro en bruto.
Si esta tecnología logra funcionar a un precio tan bajo como el que prevén sus creadores, podría convertirse en una estrategia para reducir las emisiones de gases de efecto invernadero de uno de los sectores más difíciles de limpiar de la economía , y que representa la mayor fuente de contaminación de la industria.
Tras seis años trabajando en la idea, esta compañía de nueve personas está pasando a su siguiente fase. Si logra cerrar con éxito la siguiente fase de financiación que tiene pendiente, la start-up planea construir una gran planta piloto para crear una célula electrolítica a escala industrial para producir acero.
Eliminar carbono
En el enfoque principal de la siderurgia actual, el óxido de hierro se coloca en un alto horno con coque, una sustancia dura y porosa derivada del carbón. A altas temperaturas, el coque se transforma en monóxido de carbono, que extrae el oxígeno del hierro. Este proceso da lugar a un metal intermedio conocido como “arrabio”, así como a residuos de dióxido de carbono que se liberan a la atmósfera.
Ente este y otros pasos del, la conversión mundial del hierro en acero emite cerca de 1,7 gigatoneladas de dióxido de carbono a la atmósfera, lo que representa el 5 % de las emisiones globales actuales de CO2, según un artículo reciente en Science . Y eso es sin tener en cuenta las emisiones del combustible necesario para encender los hornos.
El autor principal de ese estudio, el científico de sistemas terrestres de la Universidad de California en Irvine (EE.UU.) Steven Davis, explica: “Los coches, los edificios y los puentes dependen del acero. Así que, a menos que cambiemos esa dependencia, algo que parece poco probable, tenemos que encontrar una forma de descarbonizar su producción”.
Pero para eliminar completamente las emisiones asociadas a la fabricación del acero hace falta una tecnología capaz de capturar el dióxido de carbono antes de que el producto salga de la fábrica. Esta opción es cara y técnicamente peligrosa, así que otra alternativa sería emplear otro tipo de materiales que eliminen el oxígeno del óxido de hierro.
Un proyecto que empezó en la Luna
Casi por casualidad, el químico del MIT Donald Sadoway comenzó a trabajar en una solución a mediados de la década de 2000.
La NASA había ofrecido un premio de unos 200.000 euros al primer equipo que descubriera cómo extraer el oxígeno de la superficie de la Luna, una capacidad necesaria para poder establecer bases en nuestro satélite. Sadoway propuso usar una celda electrolítica, que produce una corriente eléctrica que descompone los compuestos. Con ella podría extraer oxígeno de las rocas lunares. Como subproducto de este proceso, el investigador se encontró con un metal fundido, un hallazgo que le llevó a explorar la idea de utilizar un enfoque similar para procesar metales en la Tierra.
Pero para producir algo similar al acero necesitaba un ánodo de materiales baratos, incapaces de corroerse a altas temperaturas, ni que pudieran reaccionar fácilmente con el óxido de hierro. En 2013, junto a Sadoway, el investigador en metalurgia del MIT Antoine Allanore, publicó un artículo en Nature en el que planteaba que los ánodos hechos de aleaciones basadas en cromo cumplían todos esos requisistos.
El año anterior, Sadoway, Allanore y otro socio habían cofundado la start-upBoston Electrometallurgical, que más tarde se convertiría en Boston Metal. Hasta la fecha, la compañía ha recaudado más de 11 millones de euros, principalmente del inversor brasileño Ingo Wender, del Departamento de Energía de EE. UU. y de la Fundación Nacional de Ciencias de EE. UU. e (National Science Foundation). Aunque la empresa tiene otra fuente de financiación pendiente, no ha querido revelar su origen hasta que no se complete la transacción.
El dinosaurio de la siderurgia
El los almacenes de Boston Metal ya hay una de sus celdas electrolíticas. Se trata de un cilindro de metal, con un tubo en forma de chimenea que emerge de la parte superior y una abertura ovalada en la parte frontal. El dispositivo está diseñado para producir ferroaleaciones, productos con un alto margen de beneficio que se usan para producir ciertos tipos de acero, que es el material diana de la empresa.
La “chimenea” es en realidad un ánodo. Y una delgada capa de metal ubicada al fondo forma el cátodo. La combinación de estos electrodos positivos y negativos actúa como una especie de bomba que impulsa los electrones, una mezcla de minerales metálicos y otros óxidos a través del electrolito dentro de la cámara.
Disponer de los ingredientes precisos dentro del electrolito es una parte crucial de la tecnología central de esta compañía. En el caso del acero, el resto de óxidos actúan como un solvente a altas temperaturas que disuelve el óxido de hierro sin descomponerse.
A medida que la corriente eléctrica calienta esa sopa, el oxígeno se libera de las burbujas de hierro hasta la parte superior, y el metal resultante se acumula en la parte inferior. Una vez que los operadores “golpean”, o atraviesan, la cubierta a través del orificio de la parte delantera, el metal fundido se vierte en forma de línea anaranjada ardiente.
Una ventaja de usar carbono para fabricar acero es que, en la proporción correcta, este elemento aporta fuerza al producto final. El director de Estrategia de la compañía, Adam Rauwerdink, afirmó en un correo electrónico que para producir acero de determinados grados, simplemente habría que añadir carbono y otros ingredientes mientras el metal se enfría.
Pero hay quien se pregunta si el proceso logrará seducir a la conservadora industria siderúrgica, que al fin y al cabo debe trabajar con un material capaz de mantener en pie los rascacielos. En otro correo electrónico, explicó el químico del Instituto de Tecnología de California (EE.UU.) Nathan Lewis, detalla: “Para obtener las propiedades mecánicas del acero en sí, en algún momento del proceso hace falta carbono. Así que resulta comprensible que la industria no esté muy convencida de cambiar el proceso”.
Un rayo de esperanza
El actual CEO de Boston Metal, Tadeu Carneiro, se unió a la compañía el año pasado. Antes de eso, lideraba la empresa CBMM, con sede en Brasil , el mayor productor de niobio, un metal utilizado para fabricar aleaciones superconductoras.
Carneiro, quien usa unas grandes y oscuras gafas oscuras, garabatea ecuaciones químicas en una pizarra mientras describe, con acento brasileño, la estrategia comercial de la compañía. Su plan a tres años es construir una instalación de demostración para producir ferroaleaciones, afirma. Mientras tanto, la compañía también comenzará a diseñar y construir una celda a gran escala para la producción de acero, un hito que espera alcanzar dentro de siete años.
Si Boston Metal logra cumplir sus objetivos, podría dar con una serie de modelos comerciales y obtener la licencia de su tecnología, asociarse con fabricantes de metal, empezar a vender sus células o producir directamente sus propios metales.
Pero como siempre en la ciencia, hasta que el producto no se construya y se pruebe a escala comercial, es demasiado pronto para afirmar que funcionará bien o que resultará económico. Además, limitarse a producir una versión ecológica de un producto al mismo precio no será incentivo suficiente para transformar la industria. Ahora mismo, el sector tiene miles de millones de euros invertidos en fábricas de acero convencionales capaces de pueden operar durante décadas. Además, gran parte de esta industria está ubicada en países relativamente pobres o con problemas financieros.
Davis concluye: “Aunque ahora mismo dispusiéramos de una tecnología perfecta, probablemente harían falta varias décadas antes de que toda la industria realizara su transición“.
Carneiro reconoce que Boston Metal aún debe superar una serie de desafíos técnicos. Uno de ellos consiste en mejorar la “eficacia de Faraday”, que implica aumentar el porcentaje de electrones que realmente producen el metal. También necesitan mejorar la eficiencia térmica o reducir los kilovatios-hora de electricidad requeridos para producir una cantidad dada del metal; y producir un ánodo de aleación de cromo funcional, una pieza que, de momento, solo han demostrado a nivel laboratorio.
Pero el responsable está seguro de que lo conseguirán y podrán que su tecnología es más barata. Y al final, lograrán convencer a la industria para que adopte su enfoque. Transformar el sector siderúrgico, valorado en casi un billón de euros todavía es una posibilidad remota. Pero si la start-updemuestra que su proceso funciona a escala industrial, se convertirá en un rayo de esperanza para resolver una de las piezas más difíciles del rompecabezas climático.
Leer más
- Una nueva forma de fabricar acero podría limpiar el CO2 de la siderurgia
- Produciendo productos cotidianos con hongos
- Con hojas de caña panelera producen descontaminante de agua
- Plantas que iluminan para sustituir a las lámparas eléctricas [VIDEO]
- Tejidos, otra manera de reutilizar las botellas plásticas
- Cáscaras de pistacho para limpiar el agua
La entrada Una nueva forma de fabricar acero podría limpiar el CO2 de la siderurgia se publicó primero en .
Seguir leyendo